Wie Roboter helfen, Kompressor-Rotoren zusammenzuschrauben
Robot Systems
-
Produkt:
RBU -
Job:
Positionserkennung von Schrauben
Das Zusammenschrauben eines Kompressorrotors erfordert viel Geduld. Dies ist eine Arbeit, die nicht überstürzt werden darf und die eine ruhige Hand erfordert. Die Mechaniker beginnen damit, die beiden Trommeln auszurichten, bevor sie 34 Muttern und die dazugehörigen Unterlegscheiben nacheinander an der richtigen Stelle anbringen. Sie ziehen die Muttern locker an und ziehen sie dann nacheinander in mehreren Schritten und mit genau dem richtigen Drehmoment an. Um sicherzustellen, dass sich das Bauteil nicht verzieht, ziehen sie die Muttern paarweise gegenläufig an. Vor und nach dem Anziehen messen sie das Drehmoment mit einem Kalibriergerät. Beim endgültigen Festziehen überprüfen sie die Selbsthaltung der ovalen Muttern – sie dürfen weder zu locker noch zu fest sein. Es handelt sich also um eine Arbeit, die von den Mechanikern viel Fingerspitzengefühl verlangt. Doch in Zukunft wird sie, zumindest bei der MTU Maintenance in Hannover, von einem Roboter durchgeführt. Das neue Verfahren automatisiert nicht nur das Zusammenschrauben der Rotorkomponenten, sondern nutzt den Roboter auch zur gleichzeitigen digitalen Dokumentation. Der erste Einsatz des Roboters wird der Hochdruckverdichterrotor für das Zweiwellen-Turbotriebwerk V2500 sein, das unter anderem die Airbus A320-Serie antreibt.
Robot Systems
-
Produkt:
RBU -
Job:
Positionserkennung von Schrauben -
Features:
- Konsistente Präzision
- Verbesserung der Prozesszuverlässigkeit
- Ermöglicht Schraubarbeiten in schwer zugänglichen Bereichen
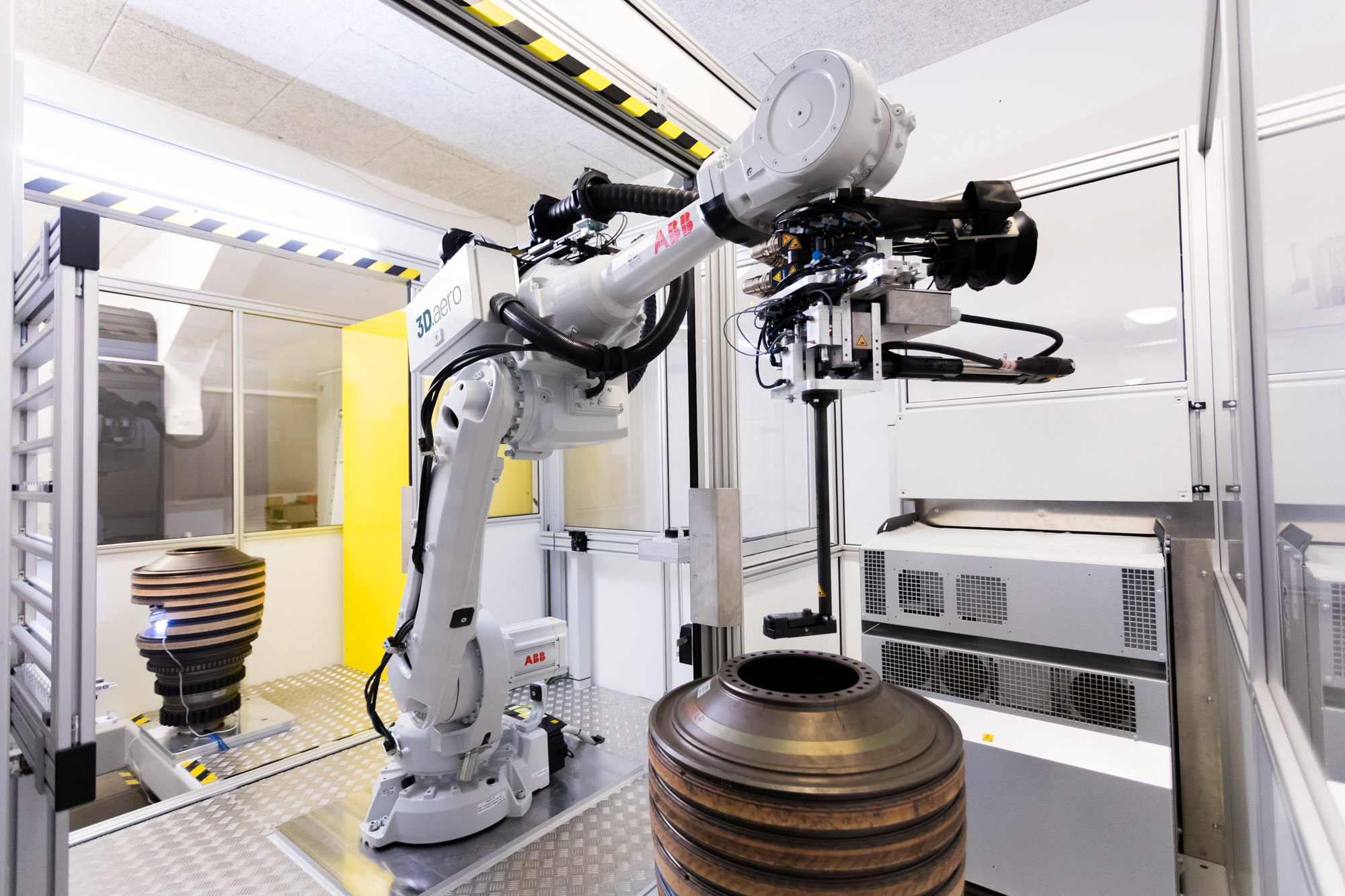
„Unser Ziel war es, die etablierte manuelle Arbeit abzulösen, da der Schraubprozess aufgrund seiner Komplexität immer fehleranfälliger wurde“, sagt Nico Vohse, der die Idee zu dem Projekt hatte und es ins Leben rief. Das Projektteam machte sich auf die Suche nach einer optimalen, zukunftsweisenden Lösung. Doch anstatt einfach einen manuellen Prozess durch einen anderen zu ersetzen, entschied sich MTU für einen automatisierten Prozess, der auf Industrierobotern basiert. Das verspricht eine gute Investition in die Zukunft: Da die neue Lösung deutlich präziser ist und sich auch auf andere Rotortypen anpassen lässt, werden mittelfristig auch andere MTU-Standorte davon profitieren.
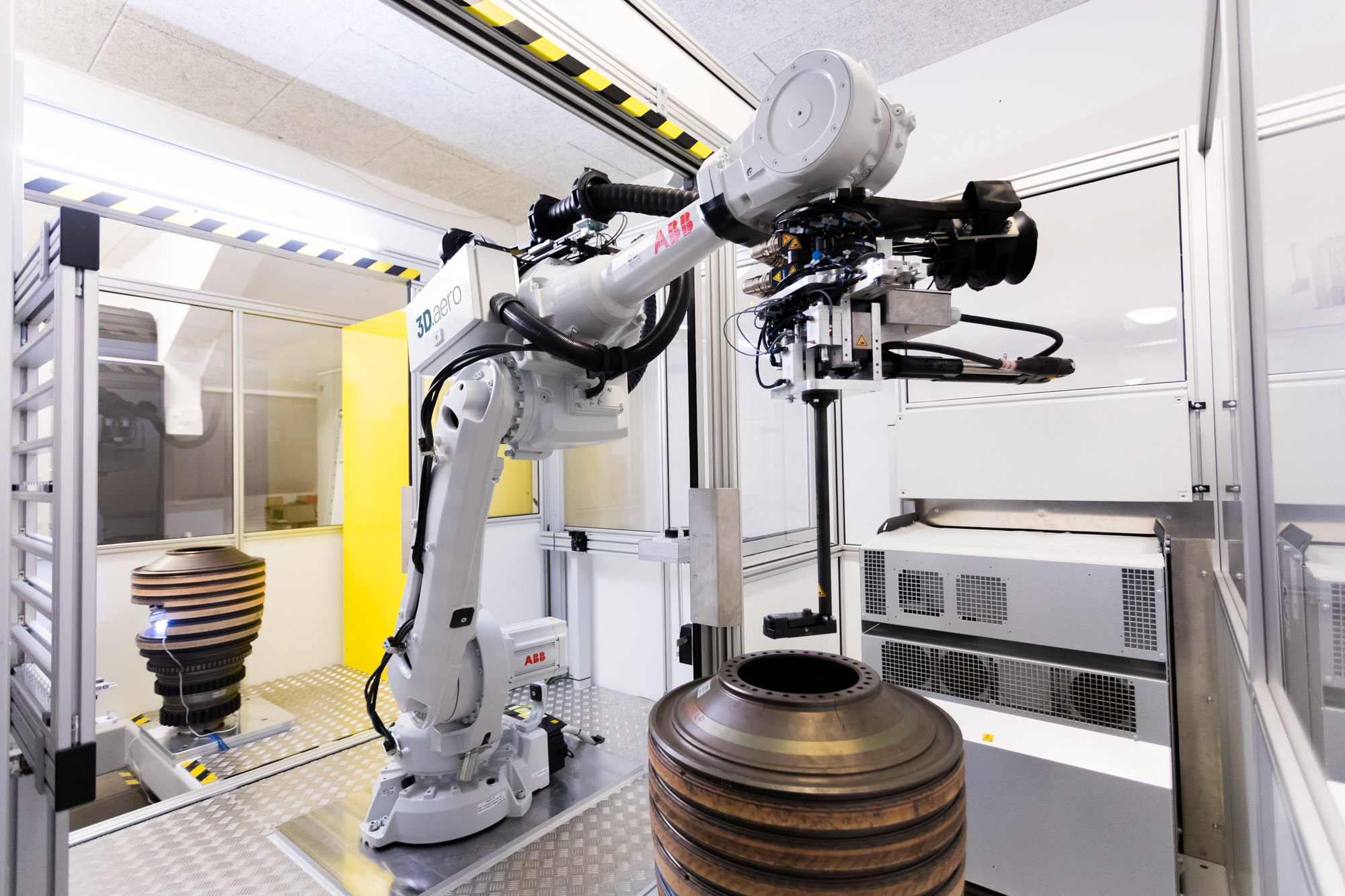
Präzision
Automatische Schraubvorgänge in schwer zugänglichen Bereichen
Effizienz
Optimierung der Prozesseffizienz
Konsistenz
Verbesserung der Prozesszuverlässigkeit
Nico Vohse – Initiator und Ideengeber des Projekts
„Unser Ziel war es, die etablierte manuelle Arbeit zu ersetzen, da der Schraubprozess aufgrund seiner Komplexität immer fehleranfälliger wurde.“
Mühsame und unergonomische Handarbeit entfällt
Mühsame und unergonomische Handarbeit entfällt
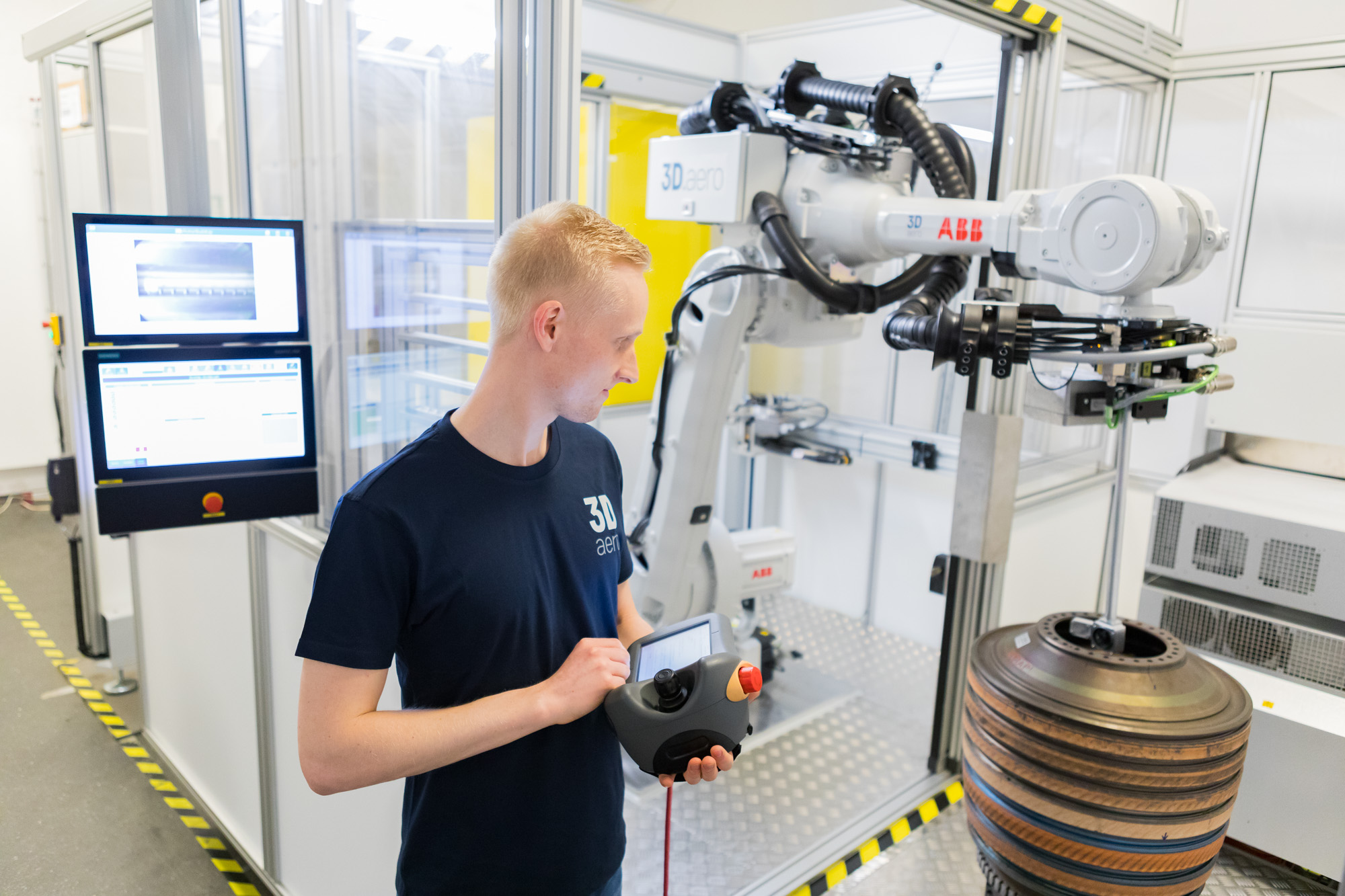
Gemeinsam mit 3D.aero – einem Anbieter von Automatisierungslösungen, der sich auf die Lösung spezieller Probleme in der Luftfahrtindustrie spezialisiert hat – entwickelte das Team aus Hannover eine Lösung, die viele Vorteile der Digitalisierung und Industrie 4.0 vereint. Auch für die Mitarbeiter, die die Arbeit erledigen müssen, ist das eine große Erleichterung. Es war von Vorteil, dass sich im Projektteam mehrere Mitarbeiter befanden, die diese Aufgabe bereits mehrfach manuell ausgeführt hatten und daher mit den Handgriffen und den damit verbundenen Hindernissen bestens vertraut waren. „Früher arbeiteten die Mechaniker in einer wenig ergonomischen Position über den Rotor gebeugt und kontrollierten schließlich mit Spiegel und Licht, ob die Muttern in der richtigen Position waren“, sagt Ingo Scheele, der im Projektteam für den First Level Support zuständig war. „Als wir auf die Roboterlösung umstellten, nutzten wir die Gelegenheit, diese unergonomischen Prozesse zu eliminieren und gleichzeitig ein Kamerasystem einzuführen, um den Schraubprozess zu dokumentieren“, sagt Vohse. Nun fährt das Kamerasystem in das Innere des Rotors und dokumentiert, ob dort alles in Ordnung ist und ob die Muttern richtig angezogen sind. Die gesammelten Bilddaten werden dann zur späteren Verwendung gespeichert. Der zusätzliche Vorteil dieses Systems besteht darin, dass der gesamte Prozess nun aus der Ferne überwacht werden kann.
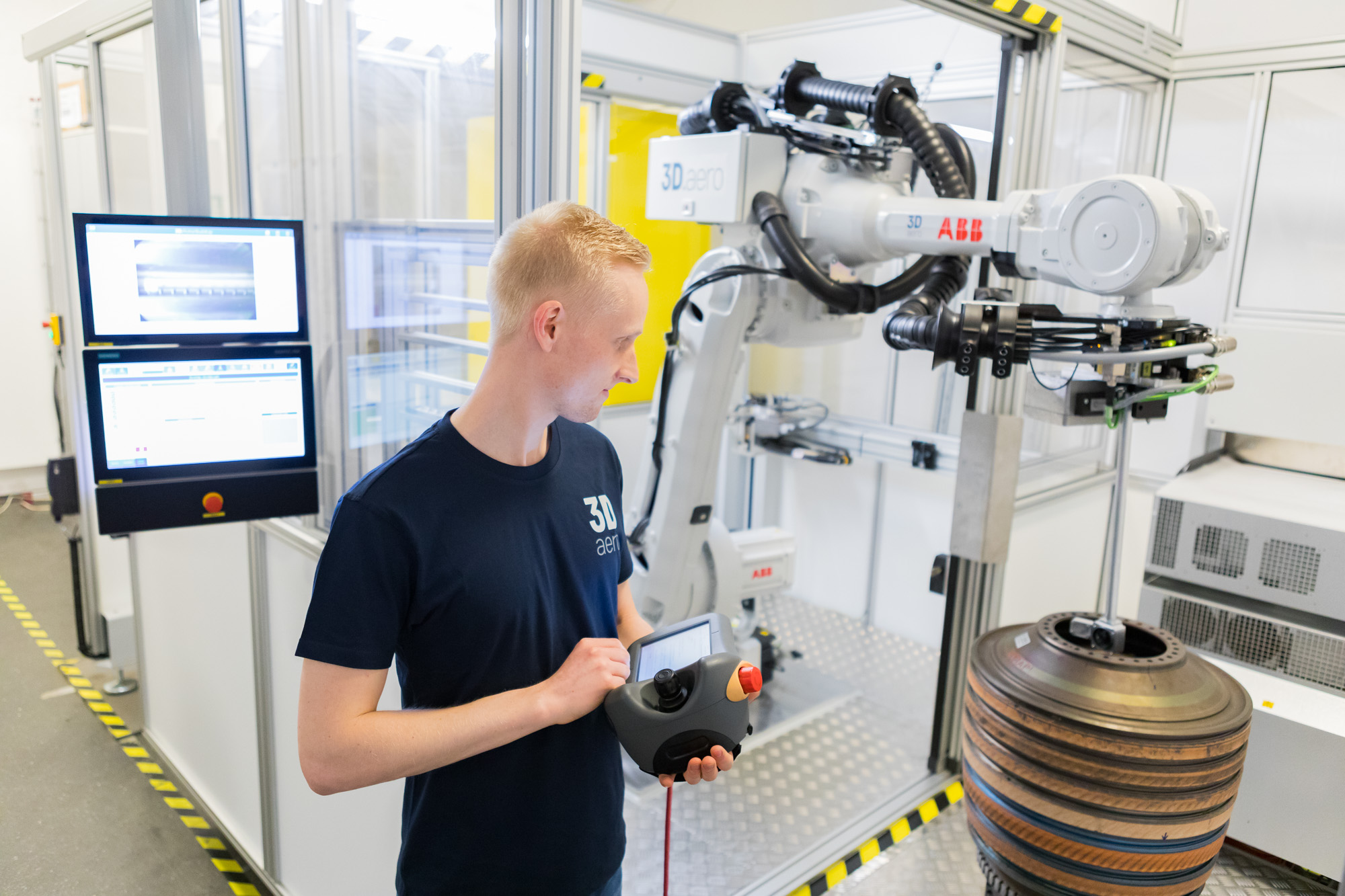
Nico Vohse – Initiator und Ideengeber des Projekts
„Stattdessen haben wir mit dem Schraubroboter einen stabilen, qualitativ besseren Prozess und einen Arbeitsablauf erreicht, der es uns ermöglicht, sowohl die Fehlerwahrscheinlichkeit als auch die Ausfallrate zu reduzieren. Schließlich liegt es in der Natur eines Roboters, eine Aufgabe präziser und mit weniger Aufwand zu erledigen als ein Mensch.“
Präzise Motormontage mit geringer Fehlertoleranz
Präzise Motormontage mit geringer Fehlertoleranz
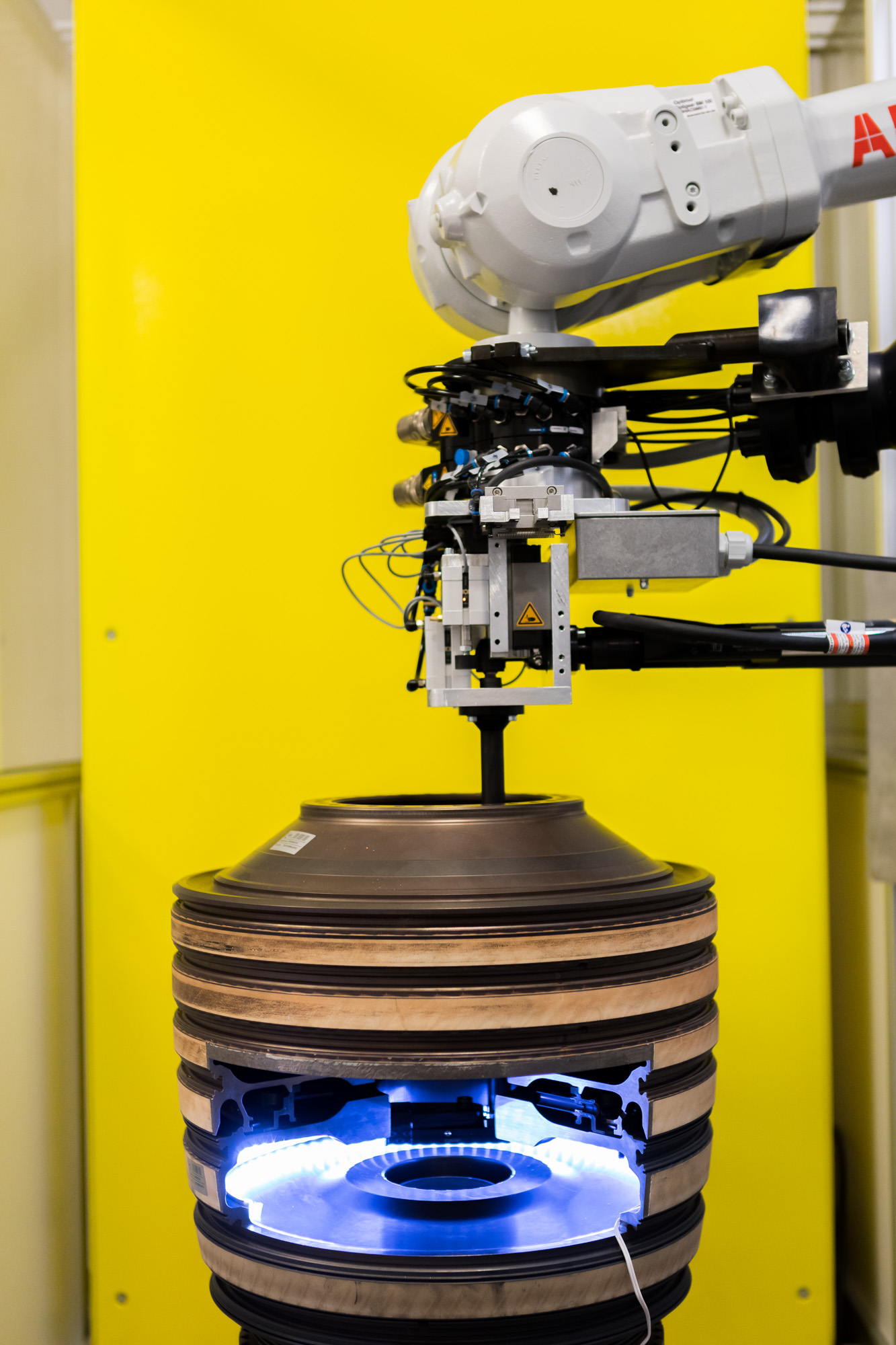
Die Verfahrensschritte und die Reihenfolge sind jedoch im Vergleich zur Vorgängerversion weitgehend gleich geblieben: das erste Aufsetzen der Muttern und Scheiben, das paarweise Anziehen, das zweite Aufsetzen mit anschließender Überprüfung der Selbsthaltung und dann das endgültige Anziehen. Die Auswahl der Muttern und Unterlegscheiben sowie deren Platzierung im Werkstück erfolgt nun jedoch vollautomatisch durch einen pneumatischen Greifarm über eine Greifwechselstation. Vor und nach dem abgeschlossenen Schraubvorgang wird mit einer Kalibriereinheit überprüft, ob das Drehmoment an den mechanischen Bauteilen den strengen Vorgaben des Motorherstellers entspricht. Ein Doppelmagazinsystem reduziert ungenutzte Montagezeiten: Während in der einen Kammer der Schraubvorgang stattfindet, wird in der anderen Kammer das Rüsten für den nächsten Auftrag vorbereitet.
Auch mit der neuen Lösung dauert es immer noch etwa zwei Stunden, einen Kompressorrotor zusammenzuschrauben. Aber Vohse merkt an, dass ein paar Minuten hier oder da kaum ins Gewicht fallen würden, wenn man bedenkt, wie lange es dauert, einen ganzen Motor zusammenzubauen. Wichtiger seien eine niedrige Fehlertoleranz und ein zuverlässiger, planbarer Prozess – weshalb eine Zeitersparnis von ein paar Minuten nie eine hohe Priorität hatte. „Stattdessen haben wir mit dem Schraubroboter einen stabilen, qualitativ besseren Prozess und einen Arbeitsablauf erreicht, der es uns ermöglicht, sowohl die Fehlerwahrscheinlichkeit als auch die Ausfallrate zu reduzieren. Schließlich liegt es in der Natur eines Roboters, eine Aufgabe präziser und mit weniger Aufwand zu erledigen als ein Mensch.“
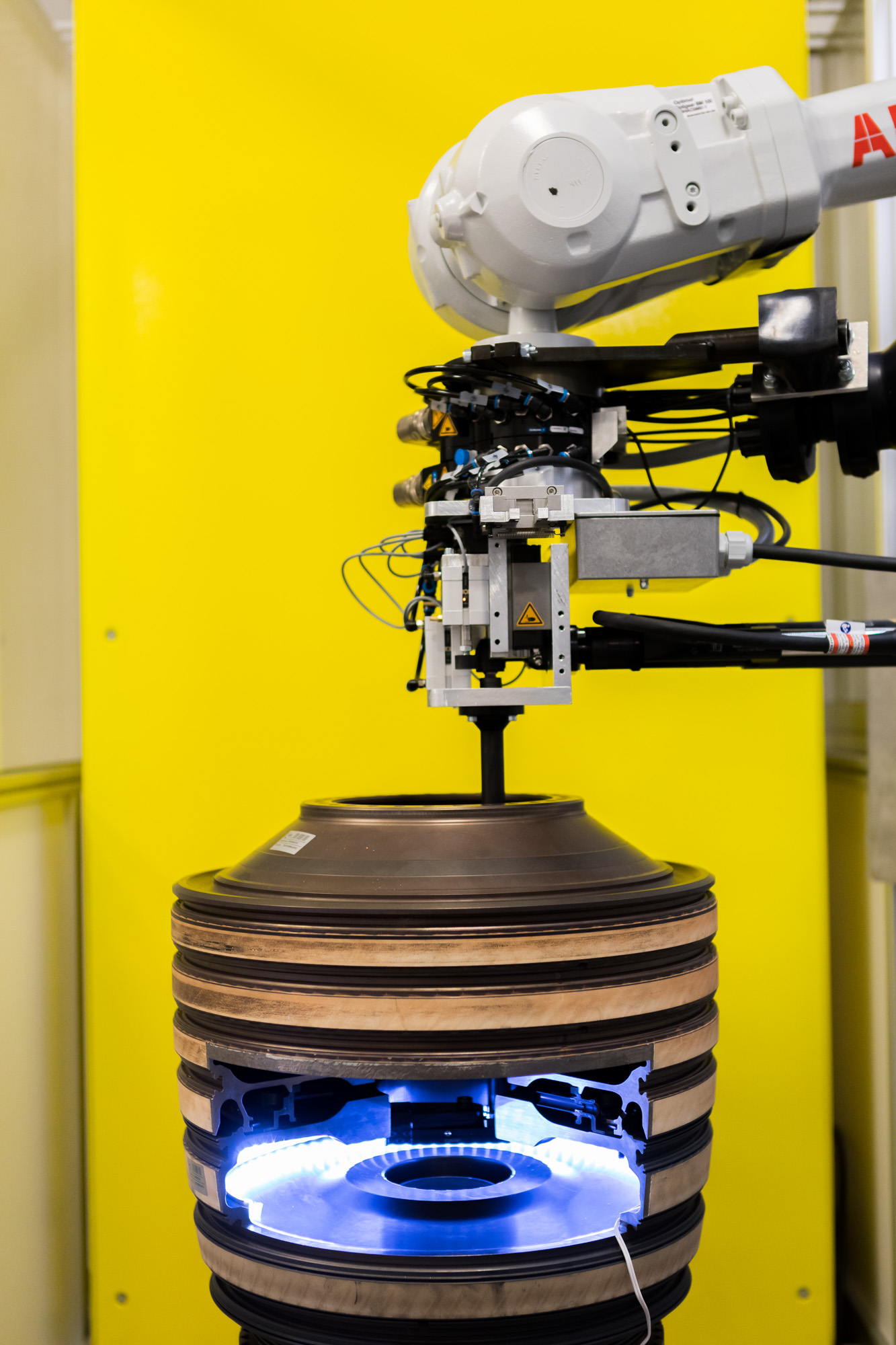
William Xu – Projekt Team Mitglied
„Am Ende des Tages ist unsere größte Errungenschaft mit dem Straffungsroboter, dass wir industrielle Systeme und IT näher zusammengebracht und einige große Barrieren eingerissen haben, von der Einbindung der IT bis hin zur Umsetzung der Industrie 4.0-Strategie von MTU.“
Flexibel an andere Kompressor-Rotoren anpassbar
Flexibel an andere Kompressor-Rotoren anpassbar
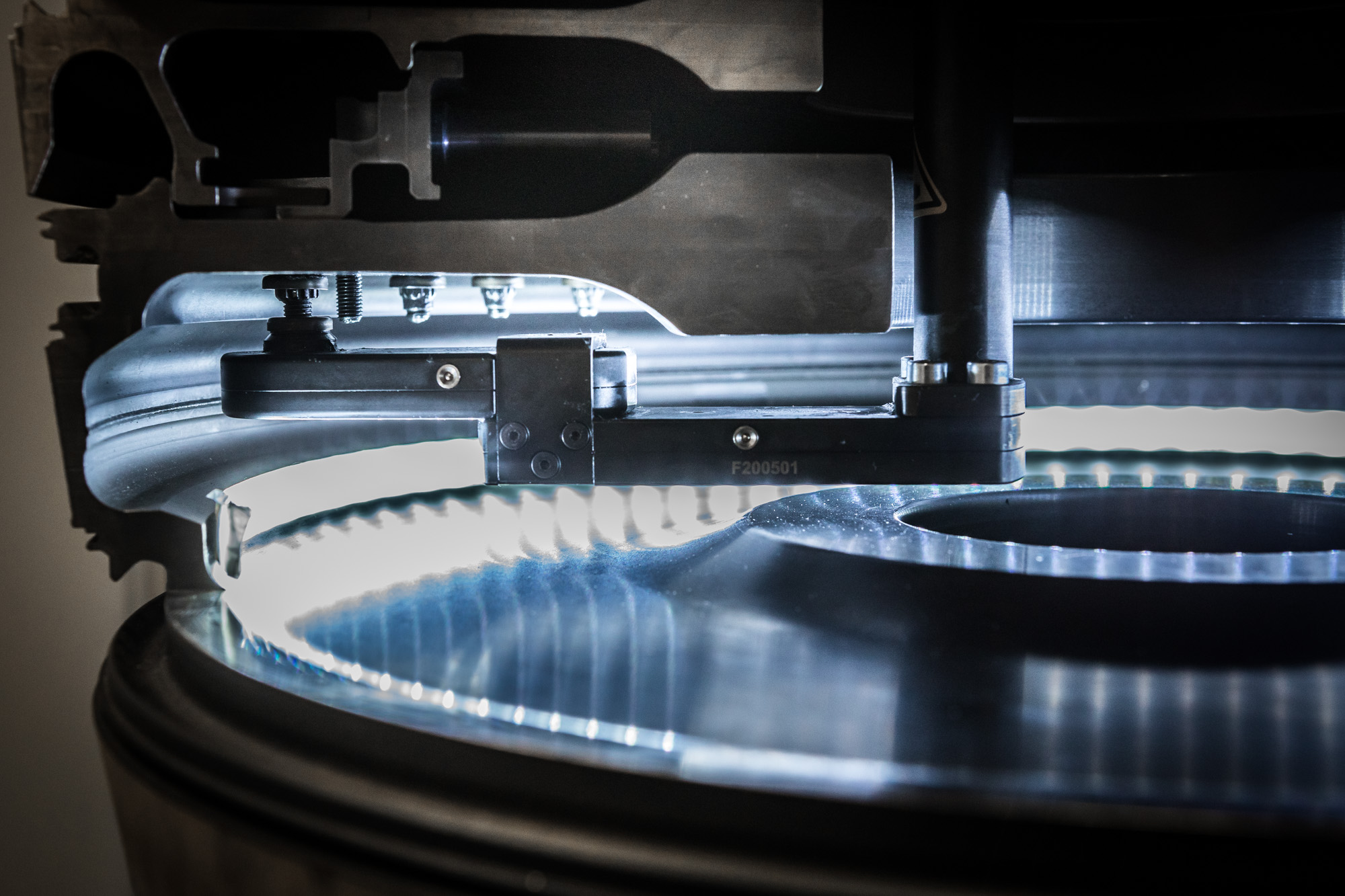
Die Lösung, die in Zusammenarbeit mit 3D.aero erzielt wurde, ist in hohem Maße maßgeschneidert – es gab keinen wirklichen Plan, dem man folgen konnte, oder einen ähnlichen Prozess. „Dies ist der erste automatisierte Schraubroboter der MTU im Bereich der Montage und Demontage, der einen so spezifischen Instandhaltungsbereich unterstützt. Es wird aber nicht die einzige Anwendung bleiben, die wir uns für diese Technologie vorstellen können“, sagt Oliver Persuhn, der gemeinsam mit Vohse das System von Anfang an mitentwickelt hat und in den Regelbetrieb überführt.
Persuhn erklärt, dass die MTU bestrebt ist, das präzisere Anziehen des Systems und die verbesserte Zeitplanung in den Instandhaltungsprozessen für größere Rotorserien zu übernehmen. „Die aktuelle Anlagenvariante kann Rotoren mit einem Durchmesser von bis zu 1,10 Metern aufnehmen. Und da der Roboter mit Schnellverschlusskupplungen ausgestattet ist, können wir das Anziehwerkzeug relativ einfach und kostengünstig austauschen.“ Darüber hinaus bietet die Technologie eine ideale Basis für ein automatisiertes Mess- und Montagesystem für größere Rotoren und andere Automatisierungsprojekte.
„Letztendlich“, so William Xu, Mitglied des Projektteams, „besteht unser größter Erfolg mit dem Schraubroboter darin, dass wir industrielle Systeme und IT näher zusammengebracht und einige große Barrieren eingerissen haben – von der Einbindung der IT bis hin zur Umsetzung der Industrie-4.0-Strategie von MTU.“ Er fügt hinzu, dass es jetzt einfacher ist, Prozessdaten in das MTU-Ökosystem zu integrieren und zusätzliche empirische Daten zu sammeln, um dieses Leuchtturmprojekt später an anderen Standorten einzuführen.
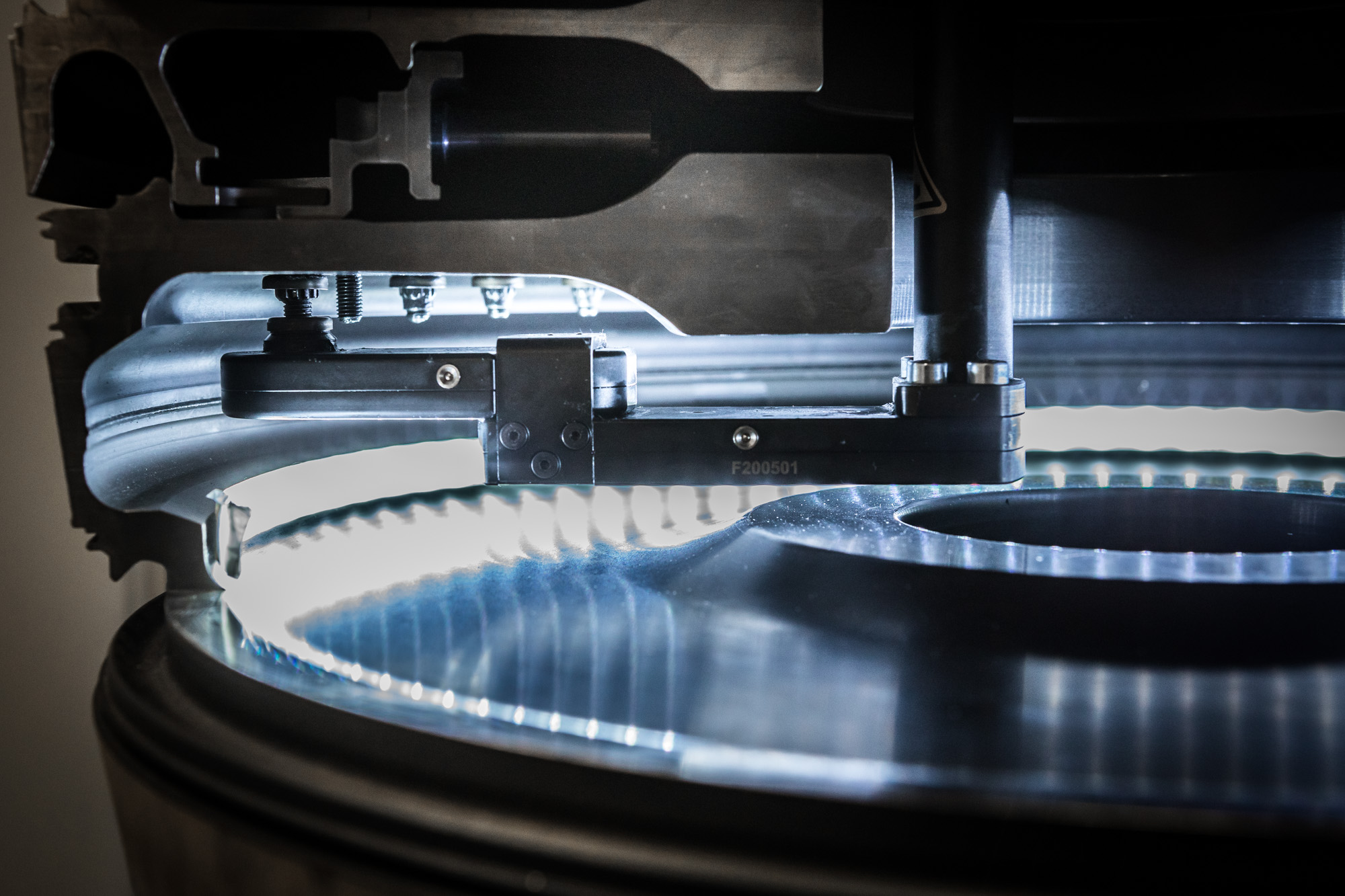
Interesse geweckt? Ich bin gerne für Sie da!
“Lernen Sie unsere praxisnahe und lösungsorientierte Arbeitsweise kennen, die mit der unkomplizierten Erprobung neuer Ideen im kleinen Rahmen beginnt und zur Umsetzung einer zertifizierten Automatisierungslösung führt.“
– Michael Ernst, Vertriebsleitung
Ich freue mich auf den Austausch!
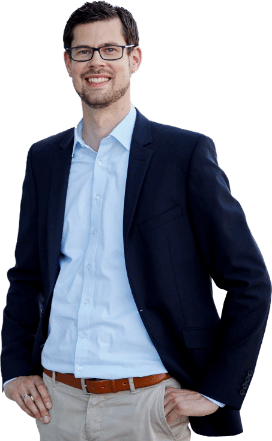